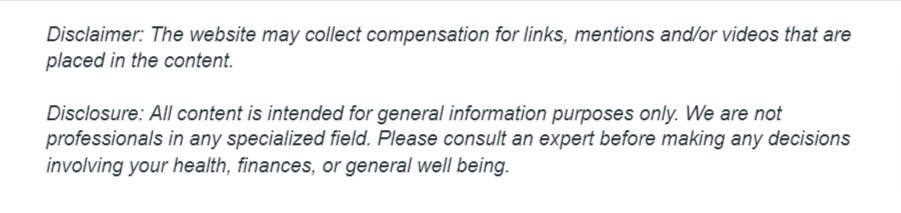

One of the most important things for any manufacturer to consider is quality control. Without effective quality control standards, a manufacturer can lose clients, and for that matter face serious consequences. Brands and companies, especially those in the food industry, depend on manufacturing systems to be reliable. In the food industry in particular, the risk for a lapse in quality control is perhaps highest in the packaging g stage. Improper food packaging systems can result in food products being mislabeled or even contaminated with things like metal. Therefore, it’s crucial that there is a system of checks and balances in place to ensure that when mistakes happen — because no matter how great the manufacturer, mistakes do happen on occasion — they are caught before the product hits the grocery stores. For that matter, there are a variety of different types of food packaging machines, and it’s important that manufacturers use those that are the most efficient and the least wasteful, especially in this day and age. Today, consumers often make choices regarding their purchases based on a product’s environmental impact. In fact, 52% of people globally make their purchasing decisions based partially off of packaging that shows a brand making a positive social and environmental impact. Below, we’ll look into some of the more effective types of food packaging, as well as the manners in which quality control can be maintained.
Efficient Versus Inefficient Packaging
As mentioned above, consumers like to see packaging that reflects a brand’s interest in reducing its environmental footprint. While it’s difficult to avoid using materials like plastic in food packaging, the manner in which packaging is used can cut down on a brand’s wastefulness. In fact, plastic itself can reduce food waste, sometimes drastically — according to packaging experts, each pound of plastic packaging can reduce food waste by up to 1.7 pounds. This is perhaps especially true in the case of vacuum-sealed packaging, which can certainly aid in reducing a food product’s risk of spoiling. For that matter, by using just two pounds of plastic, a manufacturer can package and deliver 1,300 ounces — or 10 gallons — of liquid beverage. Comparatively, you would need three pounds of aluminum, eight pounds of steel, or over 40 pounds of glass to do the same thing. For that matter, by participating in and encouraging consumers to participate in plastic recycling programs, a brand can further reduce its negative environmental impact, and even contribute to positive social change.
Checkweighers And Quality Control
When delving into quality control issues, it’s important to take note of the variety of different in ways through which quality products are maintained. When it comes to packaging itself, checkweighers are crucial to most quality control systems. Checkweighers are types of machines — automatic of manual, depending on the type — that are used to check the weight of packaged commodities. Normally, it is used at the offgoing end of a packaging process. It ensures that the weight of the packaged product is within certain limits. It the weight is too much or too little, they will be taken out of a line automatically. Checkweighers ensure that a consumer will get exactly what they’re paying for, and cut down on the risk of human error in the manufacturing process. They also can signal the presence of certain, unusual contaminants — if a product weighs too much, this is certainly a risk.
Food X-Ray Machines And Contaminants
Some — in fact, most — contaminants are too small for the human eye to notice, which is why it’s important that food x-ray machines are used to scan for things like metals. Typically, there are three different types of metal contaminants that a food x-ray machine can notice: ferrous, non ferrous, and stainless steel. While some of these metals are so small that a consumer might not even notice them, they are nonetheless dangerous, and the x-ray process should be taken seriously.